In the BHS HOT AIR® heat staking processes, the process steps of heating and forming are separated and can thus be carried out in parallel by two modules in two stations. This allows the cycle time of the machine to be significantly reduced. A particular advantage of this process is that it always ensures consistently good riveting results without melt leakage, even over high volume fluctuations due to component tolerances.
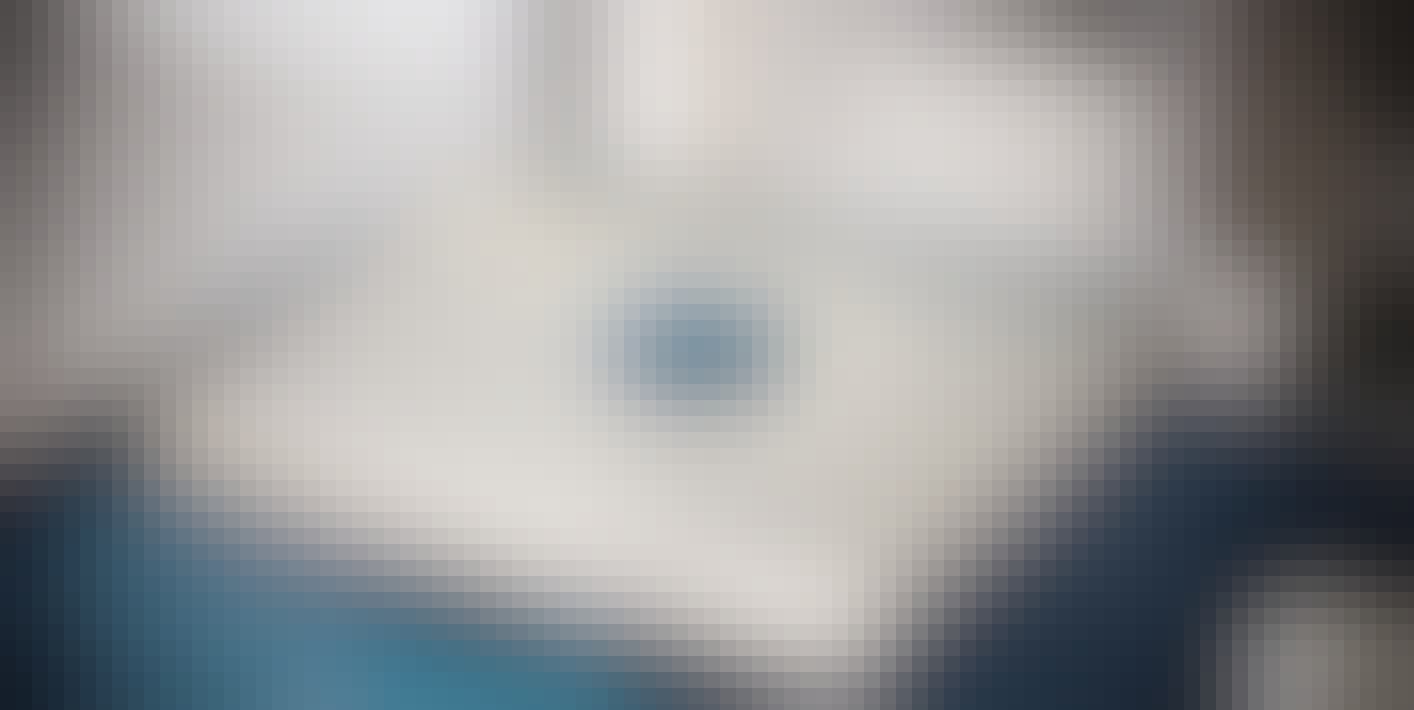
Srcoll
Heat staking methods
BHS HOT AIR®
The BHS HOT AIR® riveting process is a two-stage joining process.
BHS HOT AIR®
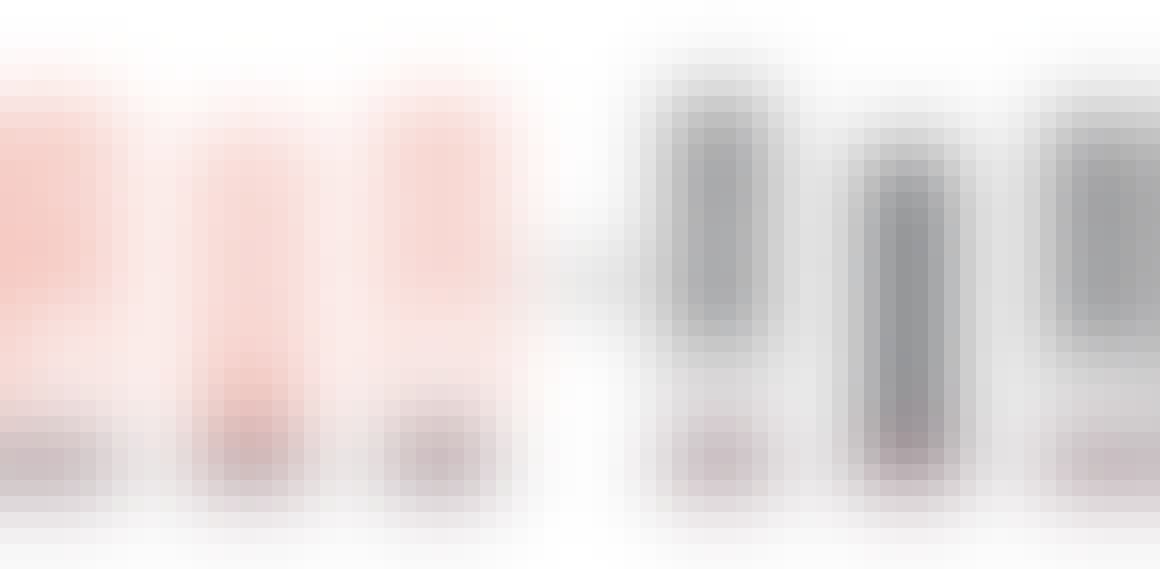
Characteristics
Hot air riveting
Redundant temperature measurement
Temperature control
Flow rate monitoring
Modular interchangeable heating and riveting assembly
Typical process times 5-10 seconds
Advantages
Fast cycle times
Multiple production possible due to tool change
Highest possible rivet strengths
Homogeneous rivet head formation
Volume-independent rivet head geometry

In the BHS HOT AIR® heat staking processes, the process steps of heating and heat staking are carried out in parallel by two modules in two stations.
Request whitepaper
Get the whitepaper with the title "How a new gap filler injection process improves pouch-cell module assembly" as a free download.
Simply enter your contact details and we will send the whitepaper to you.
Heat staking machines
We have the right heat staking system for your requirement from low production volumes to fully automated series production.
Heat staking
Technology Center
Benefit from our expertise and many years of experience and develop the optimum process for your requirement together with us. We are specialists for different heat staking processes.
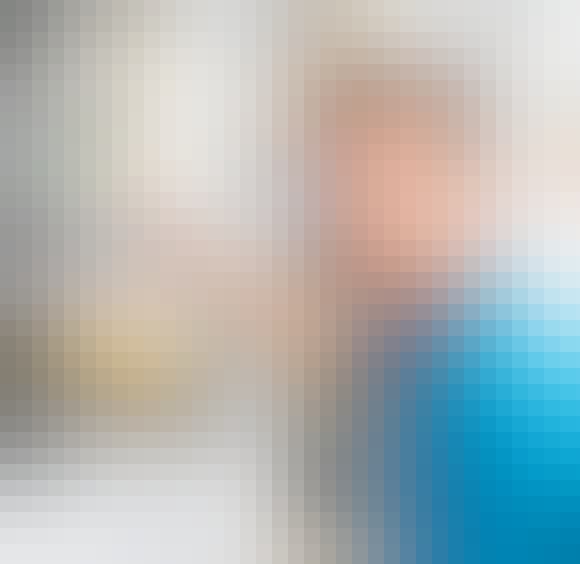
Request Design Guideline
bdtronic offers standard tools that represent an optimal riveting as a compromise between low cycle time and maximum strength. Request our design guidelines today!