Electrification in the automotive sector continues to advance and is causing a profound change in the industry. There are different types of drive concepts: battery electric vehicles (BEVs) as purely electric drives, hybrid drives (HEVs) that have both an internal combustion engine and an electric motor, plug-in hybrids (PHEVs) that, unlike HEVs, can be charged via a power socket or rapid charging systems, and range-extended electric vehicles (REEVs).
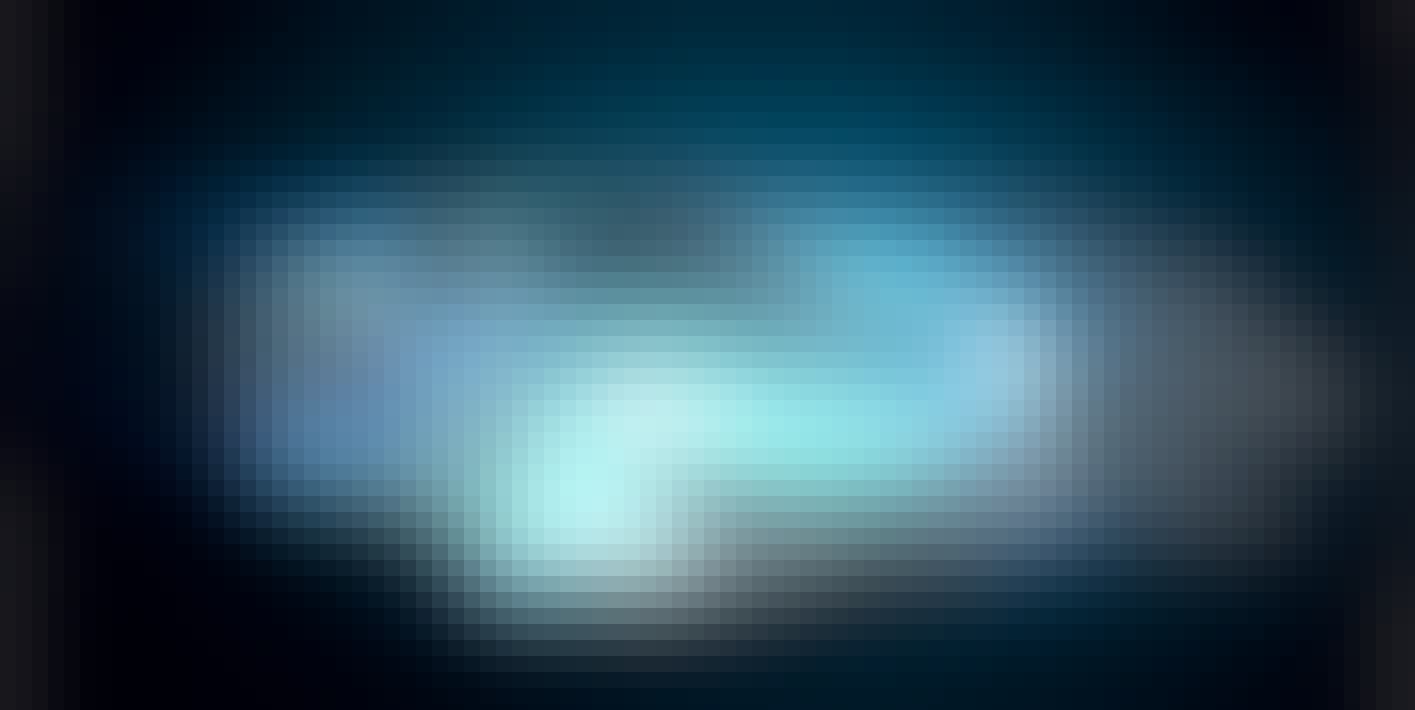
Srcoll
Dispensing applications
Electromobility
Electromobility is the future of mobility. bdtronic offers solutions for dispensing applications for all important components of electric vehicles.
High-voltage battery, high-voltage storage unit
Alongside the electric motor, the high-voltage battery or high-voltage storage unit is the heart of an electric car or hybrid vehicle. It supplies the electric motor with power and also serves as an energy storage device. The battery pack consists of several battery modules, which in turn consist of a large number of battery cells.
The battery cells must be firmly bonded together to achieve their performance. The adhesive bond between the battery cells is applied with our dispensing equipment. This dispensing process enables cost-effective and fast assembly of prismatic, cylindrical or pouch cells. To achieve the best possible and longest lasting adhesion, the battery cells are pretreated with plasma using our plasma systems to activate and clean the surface before the adhesive is applied.
The battery modules generate energy in the form of heat during operation. This is dissipated by applying thermally conductive materials between the battery module and the aluminum cooler to prevent overheating. The battery modules are mounted in a housing and then sealed with a lid. To prevent moisture from entering the battery housing from the outside, a liquid seal is applied between the lid and the housing.
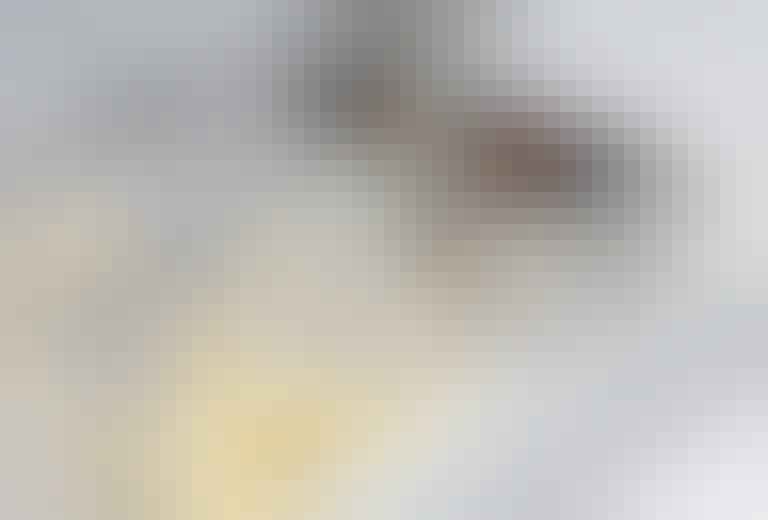
Thermal conductive pastes are applied between battery modules and aluminum radiators to prevent overheating.
Battery management system
Every high-voltage storage system has a battery management system (BMS). This central control unit monitors and regulates the state of the battery. The BMS determines the current state of charge of the battery, regulates cell balancing, prevents short circuits and handles communication with the vehicle.
To prevent moisture from entering the battery management system, a liquid sealant is applied between the housing and lid using our dispensing system. Beforehand, the housing and lid are pretreated with plasma to increase the surface tension of the lid and housing and improve the adhesion of the adhesive. To fix the PCB in the housing, it is riveted in the housing by our Heat staking technology.
Battery Junction Box
The Battery Junction Box or Power Distribution Unit (PDU) is a switching unit for the battery of an electric vehicle. It provides the power supply between the battery and the electronic components in the vehicle or disconnects them in an emergency. In the event of an accident, there is no high voltage in the vehicle and the emergency services can work safely.
The electronics inside the battery junction box must be protected against environmental influences such as moisture. For this purpose, it is encapsulated with our dispensing systems. To prevent moisture ingress, a liquid seal is applied to the BJB housing.
Power Electronics
In an electric or hybrid vehicle, the power electronics is one of the central components. The power electronics consist of a DC/DC converter and an inverter. The inverter functions as an inverter in an electric car. On the one hand, it converts the AC voltage of the electric motor into DC voltage so that the battery can be charged. A second function is to supply the electric motor with energy by converting the DC voltage of the high-voltage storage unit into AC voltage. The DC/DC converter transforms the battery's DC voltage into a lower DC voltage to supply the vehicle's electrical system with energy.
The connectors of the DC/DC converter and inverter must be protected against moisture ingress. For this purpose, the connector is potted with a potting compound. To prevent moisture from entering between the housing and the cover of the converter and inverter, a sealing bead is applied. To prevent overheating of the converter and inverter, a thermally conductive paste is applied between the circuit board and the aluminum heat sink to dissipate the energy generated in the form of heat.

The dispensing of thermally conductive and electrical insulation materials for electric vehicle inverters is a critical process.
Electric motor
The drive motors in an electric car are usually so-called AC motors, which consist of a rotor and stator. A distinction is made between asynchronous and synchronous motors. Asynchronous motors are characterized by their simple design, but have the disadvantage compared to synchronous motors that they have a significantly lower power density. Since they are also more efficient, synchronous motors are predominantly used in electric cars.
The interconnection ring of a hybrid stator has various busbars that must be protected against environmental influences and electrical flashovers. This is ensured by encapsulating the circuitry and busbars. The interconnection on the stator is mechanically fixed with a hot rivet joint. More about heat staking applications
The copper windings of the stator are insulated to increase heat dissipation, improve performance and prevent short circuits. More about impregnation solutions
On Board Charger (OBC)
The battery of an electric car must be charged with direct current. However, most household and industrial sockets and the usual charging stations use alternating current. The on-board charger in the electric vehicle converts the alternating current into direct current.
The internal capacitors of an on-board charger generate heat. To dissipate this heat and prevent overheating, a heat-conducting paste is applied between the capacitor and the aluminum housing.